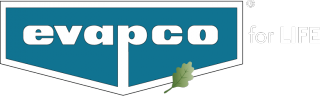
The Extra-Pak® Ice Coil by EVAPCO represents the first major technological advancement of thermal storage systems equipment in many years. EVAPCO ice coils are constructed of high quality steel and
EVAPCO’s high-efficiency thermal ice storage systems are ideal for all types of large, energy saving, thermal storage systems.
Ideal for urban installations and retrofit projects where real estate or building space is at a premium.
The Extra-Pak® Ice Coil by EVAPCO represents the first major technological advancement of thermal storage systems equipment in many years. EVAPCO ice coils are constructed of high quality steel and