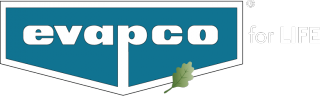
Cooling Towers
Where can I find the Full Load Amps (FLA) of a cooling tower’s electrical components?
A unit’s motor full load amps (or FLA) can be found in the technical data sheet for each specific cooling tower. It is also located in EVAPCO’s custom selection software, Spectrum, in the returned results table. To determine the FLA for other electrical accessories, please contact the HVAC marketing team. If multiple components are utilizing different voltages, the FLA will need to be broken out for each voltage.
How do I clean my air inlet louvers?
Cooling towers can often experience mineral/scale buildup on the exterior surfaces of their air inlet louvers. Improper water treatment, insufficient bleed rates, and/or excessive cycling of the fan motors are the most typical causes. Since the louver material is constructed of lightweight PVC, it cannot withstand the rigors of heavy mechanical cleaning. Therefore, DO NOT USE A WIRE BRUSH OR PRESSURE WASHER TO REMOVE THE MINERALS/SCALE FROM THE AIR INLET LOUVERS. This method of cleaning will damage and/or destroy the louvers.
The best method of removing the minerals/scale from the air inlet louvers is very simple: Remove the louver assemblies and let them soak in the cold water basin of the unit. The water treatment chemicals in the unit will neutralize and dissolve the mineral buildup. The time required for soaking the inlet louvers depends on the severity of the buildup. For more information, please contact your local EVAPCO sales representative.
What are the benefits of a belt drive system when compared to a gear box drive system?
A belt drive system brings many advantages including lower upfront costs, simplified maintenance, lower replacement costs, and shorter lead time.
Regarding maintenance, belt drive systems are much easier to service than gear box drive systems as they require no special tools, equipment, or skills. EVAPCO cooling towers feature extended lube lines—as standard—making it a simple process to grease the bearings. Gear drive maintenance comes with a higher replacement component cost, longer lead time, and advanced equipment requirements (since this process typically involves a crane).
For more information and assistance deciding which system is better for your cooling tower application, please contact your local EVAPCO sales representative.
What is the minimum recommended fan speed for an open cooling tower?
EVAPCO recommends a minimum fan speed of 25% for each available open cooling tower. Operating below 25% of motor speed achieves very little return in fan energy savings and capacity control. This recommend also applies to closed circuit coolers and evaporative condensers. If you have additional questions about the operation of your cooling tower, please contact your local EVAPCO sales representative.
Why would I use equalizer connections instead of a flume box?
Water equalization is required anytime there are two or more separate basins that are combined on the same condenser water loop. There are two main types of equalization: flume box or external equalizer pipe. Only one of these options is required.
The default equalization method for multi-cell units is a flume box.
The decision on whether to use a flume box or equalizer is typically determined by the person designing the system. External equalization requires pipework to be run (by others) between equalizer connections and is typically installed with a valve in the piping to facilitate hydraulic isolation of cells.
In contrast, to isolate cells with a flume box, a flume plate needs to be installed inside the cooling tower, under the water line, each time isolation is required. If you have additional questions about your connections, please contact your local EVAPCO sales representative for assistance.
Fluid Coolers
What is a dry bulb switchover temperature?
A dry bulb switchover temperature refers to the temperature at which a closed circuit cooler can run fully dry (with just the fans running, without the spray pumps on) and reject 100% of the design heat load. This is an important term in the engineering community as a higher dry bulb switchover temperature results in reduced water consumption throughout the year.
Since the process fluid is contained within a steel coil, when ambient conditions are colder than the dry bulb switchover temperature, closed circuit coolers can utilize airflow over the coil to achieve the required heat rejection with just the fans operating.
When a fluid cooler is sized for a dry bulb switchover temperature, this means that the pumps are off and the fans are running at 100%.
Hybrid coolers utilizing coils with extended surface fins can achieve much higher dry bulb switchover temperatures due to the additional surface area on the coil.
EVAPCO eco-coolers utilize finned coil technology and can achieve dry bulb switchover temperatures for full load (95/85/78 degrees F design conditions) up to 45 degrees F. EVAPCO eco-Hybrid coolers can achieve dry bulb switchover temperatures for full load (95/85/78 degrees F design conditions) up to 65 degrees F.
Can I operate my closed circuit cooler recirculating pump on a VFD?
No, the recirculating pumps supplied on EVAPCO closed circuit coolers are ON/OFF and require full flow to maintain system efficiency and prevent premature scaling of the coil. They are not designed to operate on a variable frequency drive (VFD).
Every fluid cooler pump is sized for a set flow rate to adequately wet the coil and provide 100% heat transfer via evaporation from the coil. If a recirculating pump is operated on a VFD at a lower speed and flow rate than required at 100%, not only will the system efficiency decrease, but premature scaling of the coil could occur from continuous wetting and drying of certain areas of the coil.
Please note that pump starters are not supplied by EVAPCO and must be provided by other manufacturers.
When should I use glycol in my closed loop system instead of water?
Glycol has antifreeze properties that protect coils in a closed circuit cooler from potential freezing during winter operation in northern climates. Glycol solutions are rarely used for closed loop systems in warmer climates, such as Florida or Arizona, unless they are being used as corrosion inhibitors.
In general, about half of closed circuit cooler applications use water and about half use glycol. Which is better for a closed loop system and why?
Water has superior heat transfer properties compared to propylene or ethylene glycol and is more frequently used in the southern half of the United States. Water is also cheaper than glycol and, in most cases, will result in a smaller unit selection while requiring less pumping HP.
In most cases, the reason to convert a closed loop system from water to glycol is to prevent freezing and the associated coil damage that results when a closed circuit cooler is exposed to lower ambient temperatures.
If water is being utilized in a closed loop system in a northern climate, it is imperative that a minimum flow be maintained at all times. The temperature inside the coil must never drop below 45 degrees F. Discharge hoods with dampers and padded insulation on the outside of the coil casing section can also help to prevent freezing of the coil if water is being used in a cooler during winter operation. The most foolproof method of protecting a coil from freezing/bursting in northern climates is to use either an ethylene or propylene glycol inhibitor which have antifreeze properties.
Reasons for not converting a closed loop from water to glycol include the capital cost of glycol (especially for larger systems), the reduced heat transfer rate of glycol (i.e., a larger unit would be required to achieve the same heat transfer capacity), and the increased pump HP required for glycol.
All of the above must be weighed when considering whether water or glycol is right for your closed loop system. For more assistance, please contact your local EVAPCO sales representative.
Where can I find the coil volume of my closed circuit cooler?
You can find the coil volume of your closed circuit cooler in 3 places. Each model’s product brochure contains this important information. Visit our comprehensive Document Library to locate up-to-date materials related to your specific fluid cooler. You may also find the coil volume in the project submittal, or within EVAPCO’s selection software, Spectrum.
If you do not have access to any of the above or the unit is an older unit and no current brochure is available, please reach out to your local EVAPCO sales representative for more information.
Please be sure to double check the following three locations for more details:
- Each EVAPCO closed circuit cooler product brochure. All current brochures can be found within this website; search the Document Library for your specific unit’s information.
- If you have access to EVAPCO’s selection software, Spectrum, coil volumes are listed with each unit.
- All EVAPCO closed circuit cooler submittals from the year 2020 and newer have a section on the technical data sheet that provides the coil volume.
Why do I need to maintain a minimum flow in my closed circuit cooler? What is the minimum flow I must maintain?
A minimum flow needs to be maintained in all closed circuit coolers to prevent potential freezing/bursting of the coil(s) during cold weather operation. Also, when the flow falls below a certain threshold it becomes laminar, which will significantly reduce performance during normal operation. The recommended minimum flow for each EVAPCO fluid cooler is located in its respective marketing product brochure. You can find all up-to-date materials in our comprehensive Document Library.
Regarding cold weather operation, the most foolproof method to prevent freezing is the use of ethylene or propylene glycol. Draining a coil should only be done in an emergency situation. Care must be taken to ensure that the piping is sized to allow the water to flow quickly from the coil. Coils should not be drained often, or for an extended period of time. Leaving the coil drained and open to the atmosphere can cause interior corrosion, which may lead to premature coil failure. Please contact your local EVAPCO sales representative or Mr. Goodtower® Service Center if you need additional assistance with winter operation/maintenance.
Water Systems
How does the quality of my site’s makeup water impact water efficiency or influence materials of construction decisions?
Water originates from various sources and can vary significantly in quality. Makeup water contains invisible dissolved minerals and insoluble matter that can impact cooling efficiency and equipment service life. These substances include dirt, minerals, gases, and microbiological organisms that, if not properly treated, can accumulate and cause reductions in heat transfer efficiency, equipment service life or increased maintenance requirements.
As heat is rejected, the water evaporates as pure H2O leaving all the dissolved minerals behind to concentrate in the basin. As fresh water is added to replace evaporated water the dissolved minerals increase, a concept known as Cycles of Concentration (COC) or Cycling Up. The quality of the makeup water directly influences how high the cycles can safely be pushed which directly impacts water efficiency.
The quality of makeup water also plays a role in selecting appropriate materials of construction for your evaporative cooling equipment. Different materials have varying levels of corrosion and temperature resistance. Poor makeup water quality may necessitate the use of more corrosion resistant materials, such as 304 or 316 stainless steels. To aid in materials of construction selection, EVAPCO® has published water quality guidelines for open cooling towers, closed circuit coolers, and evaporative condensers that can be reviewed when making decisions on materials of construction:
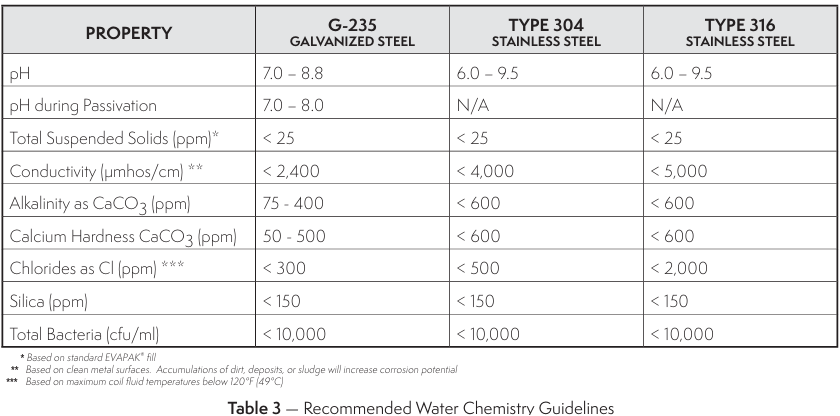
Ultimately, understanding your makeup water quality will not only allow you to run your evaporative cooled system more efficiently by optimizing your cycles of concentration, but can also help extend your equipment’s service life by selecting appropriate materials of construction.
For more information, please contact your EVAPCO® Sales representative or [email protected].
How does the need for immediate heat load affect galvanized steel coils?
For decades, the evaporative cooling industry has relied on galvanized steel as a preferred material of construction due to its cost effectiveness and thermal performance.
Galvanized zinc provides corrosion protection for the underlying carbon steel. This zinc layer is both a protective layer and acts as a sacrificial anode when any damage or breaks occur. When properly passivated, new galvanized steel can provide significant corrosion resistance to extend the service life of the steel.
Given sufficient contact time in the atmosphere, the outer layer of newly galvanized steel will naturally passivate. This passive layer protects the zinc from a form of premature corrosion known as White Rust.
Many projects lack the time to allow this passivation process to occur naturally in the atmosphere before needing to start their evaporative cooling equipment under heat load. The need to operate the equipment wet increases the potential for White Rust formation. A field passivation is often required to create the surface reactions required to form a passive oxide layer on a new galvanized coil. Properly passivating new galvanized coils is more difficult when immediate heat load is required since elevated temperatures increase corrosion potential. Once white rust forms, it cannot be eliminated, which can create both short and long-term problems.
To improve real world passivation plans for evaporative cooling equipment commissioned with immediate heat load, EVAPCO® engineered an enhanced 2-step passivation solution to minimize white rust for galvanized equipment, Pass Protect ®.
To learn more about our Pass Protect ® offering and how to best commission your galvanized coil, please contact your local EVAPCO® sales representative or [email protected] .
What are the environmental, health & safety benefits of non-chemical or solid chemical water treatment programs for evaporative cooled systems?
EVAPCO® Water Systems offers advanced water treatment programs tailored to the specific needs of evaporative cooling systems, considering factors such as makeup water quality, unit type, and location. Two key solutions, Pulse~Pure® and Smart Shield®, are available for open cooling towers, closed circuit coolers, and evaporative condensers. These systems can be installed in the field or factory-mounted on coil products.
Pulse~Pure® is a non-chemical treatment system, while Smart Shield® uses solid chemistry. Both options provide significant benefits for environmental, health, and safety (EHS) compared to traditional liquid chemical treatment. By eliminating liquid chemicals, these systems reduce the costs and risks associated with shipping, handling, and storing liquid chemicals. Additionally, Pulse~Pure® systems may not require blowdown to a sanitary drain since no hazardous chemicals are added to the water.
These technologies also support environmental sustainability by lowering carbon footprints associated with the manufacturing and transportation of liquid chemicals. Solid and non-chemical treatments require less storage space and are easier to transport, making them ideal for challenging locations like rooftops application.
Both Pulse~Pure® and Smart Shield® come with the first year of startup and service included to help ensure optimal performance. For more information or to determine how to either Pulse~Pure® or Smart Shield® to your application, contact your local EVAPCO® Sales Representative or [email protected].
What risks, if any, are associated with using municipal reclaim, rainwater or softened water as makeup for my evaporative cooled system?
Questions regarding alternative makeup water sources for evaporative cooling have become more prevalent due to water scarcity and water usage concerns. These alternate sources of makeup water can be evaluated if the system is designed to provide consistent makeup water quality to the evaporatively cooled system. The following should be considered during the design please to minimize the potential for adverse impacts in terms of water efficiency or equipment service life.
Municipal reclaim water quality tends to be more variable compared to city or well water makeup. This variability in water quality can complicate the treatment program for the evaporative cooling system and often requires additional testing and control. Variations in ammonia, bacteria, chloride, fungi, organic and oxidant lo9ading, and phosphate should be planned for and controlled.
Rainwater harvesting may be appropriate to reduce potable water usage provided the system is designed to capture rainwater and blend it into the makeup in a controlled manner. In addition to storage tank capacity, these systems often require supplemental controls for consistent blending with potable water, filtration to reduce total suspended solids, metering, microbiological control and/or testing, and supplemental pumping. A professionally designed system is more complicated than simply dumping rainwater into the cooling system when it is available.
Water softeners are sometimes considered to reduce calcium and magnesium hardness to increase water efficiency (cycles of concentration). When considered, the water required to regenerate the softeners should be included in the preliminary analysis. Split-stream sodium zeolite softening may be a cost-effective way to reduce scaling potential. EVAPCO® does not recommend the use of 100% softened water for evaporative cooled systems. Equipment manufacturers, including EVAPCO, suggest that the cooling water have at least 30- to 50 ppm of calcium hardness (as CaCO3) to protect the cooling equipment. If split-stream sodium zeolite softeners are utilized, the treatment program should be cautious in terms of cycled alkalinity, chloride and pH in the cooling water.
While alternative water sources can enhance sustainability, their use does not offer a ‘free lunch’. A careful analysis should be undertaken to understand the requirements in terms of treatment feed and control, supplemental equipment, and additional testing associated with implementing the use of alternate water for makeup to evaporative cooled systems. The treatment program should detail how the system will mitigate additional corrosion, microbiological growth, operational variability and scaling potential associated with non-potable water use. Please refer to your manufacturers’ IOM for water quality guidelines and recommendations when considering alternative makeup water sources.
Without increasing my system’s cycles of concentration, how can I reduce blowdown and makeup water demand?
Water is required for energy efficient evaporative cooling commonly used in HVAC, refrigeration, and industrial process cooling systems. Water demand for these cooling systems can be significant. As the global water crisis grows, reducing water usage in these systems becomes more and more important. EVAPCO’s industry’s leading dry and adiabatic product lines offer significant water savings, but how can end users save water when evaporative cooling solutions are required or desired?
Water usage in [evaporative cooled systems] comes from two main sources: evaporation and blowdown. Evaporation is dictated by heat load and ambient conditions, neither of which can be reasonably changed.
Total water use and efficiency in an evaporative unit can be controlled by increasing, or decreasing, the system’s “cycles of concentration” (COC). The figure below shows the relationship between blowdown and COC, the lower the COC, the higher the blowdown and greater the water consumption.
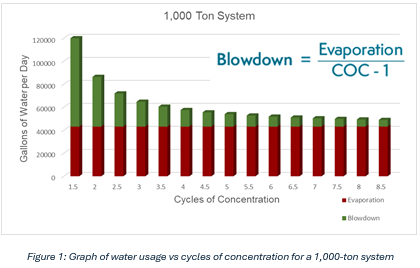
Cycles of concentration is the concentration ratio of dissolved ions in the recirculated water compared to the same dissolved ions in the makeup water. For example, if your recirculating water contains 250ppm of Chlorides and the makeup water contains 50 ppm of Chlorides, your system is operating at 5 COC. Every evaporative cooling system has a maximum safe operating cycles of concentration based on the materials of construction and makeup water quality. To increase water efficiency beyond this maximum level, thus saving water, pretreatment technology can be applied. The most common pre-treatment approaches in the industry are water softeners and reverse osmosis (RO), which can both come with application risks. EVAPCO® developed Water Saver ® as an eco-friendly, pretreatment system to improve water efficiency in evaporative cooling equipment.
Water Saver® utilizes Capacitive Deionization (CDI) technology to remove charged ions from a water supply. This technology reduces the dissolved ion concentration from the makeup supply, thus lowering the makeup water conductivity allowing your recirculating water supply to operate at higher COC. In addition to reducing your overall water usage, this technology can significantly reduce treatment chemical use rates.
To learn more about your local water quality, optimizing system efficiencies and if Water Saver ® may contribute to significant water saving at your project, please contact your local EVAPCO representative or [email protected].
Parts & Maintenance
Can EVAPCO provide replacement parts for another manufacturer's cooling tower?
Yes. EVAPCO can provide replacement parts for any piece of cooling equipment you have onsite. For specific parts and pricing (or custom requests), please contact your local sales representative.
EVAPCO has been offering parts for non-EVAPCO cooling equipment for many years. We have a dedicated Custom Design Team, as part of our Mr. Goodtower® division, that can evaluate and design parts or sections for any piece of equipment you have on your jobsite. From motors to fans, drift eliminators, louvers, pumps, sheaves, belts, or even complete rebuild kits, our team has exactly what you need for your replacement project. When you work with EVAPCO, you not only get the parts you need, but also, you get the support of our entire company.
Learn more about our Mr. Goodtower® offerings here.
How long (in general) does cooling tower fill last?
Typically, heat transfer media (otherwise known as fill) will need to be replaced once or twice during the life of a cooling tower.The longevity of fill, or heat transfer media, is predominantly a function of water and air quality, as well as proper operation. If you believe you need replacement fill or would like more information on this subject, please contact your local EVAPCO sales representative.
I need to improve the maintenance access to my cooling tower, condenser, or fluid cooler. Can EVAPCO custom fabricate ladders and service platforms to fit my installation requirements?
Yes, we can! Our representatives will work with you to provide a ladder and/or service platform designed to meet your needs and budget. The Custom Design Team within our Mr. Goodtower® division is able to fabricate solutions, even for non-EVAPCO equipment.
Our goal is to provide safe and secure serviceability for your equipment. Don't put off routine maintenance to your cooling tower, condenser, or fluid cooler because of access issues. Contact your local EVAPCO sales representative today to talk about your options.
My cooling tower is not functioning as well as it did when it was new. Is this normal? How do I get it running back to normal?
Over time, cooling tower performance can degrade due to a variety of factors. This is completely normal; however, your local EVAPCO sales representatives can help to improve operation. Our team of representatives and Mr. Goodtower® Service Centers are experts in cooling equipment and replacement parts.
If you notice any potential issues or inefficiencies with your EVAPCO or non-EVAPCO unit, contact your local representative for a free inspection or call (410) 756-2600 for assistance.
Troubleshooting
My cooling tower is overflowing because the mechanical float valve is stuck open. What should I do?
The mechanical float valve that EVAPCO uses operates with a makeup water pressure between 20 and 50 psi. When the makeup water pressure exceeds the 50-psi limit, the makeup valve will not close. The reason for this is that the buoyant force of the float ball and arm mechanism cannot overcome the force that the water pressure exerts on the valve. Therefore, when the water pressure force is greater than the buoyant force, the float ball is forced down and the valve stays open flooding the cold water basin. In addition, the excessively high water pressure will wear out the valve seat.
The solution to this problem is to simply add a pressure reducing valve (PRV) to lower the makeup water pressure to below 50 psi. Keeping the makeup water pressure to the cooling tower between 20 and 50 psi will ensure adequate operation of the mechanical float valve.
For additional troubleshooting assistance, please contact your local EVAPCO sales representative.
My tower was just installed and there is rust around the basin. What can I do?
If the unit was just installed, the rust is probably not affecting the integrity, or life expectancy, of the base stainless steel material. It is most likely foreign material on the surface that can be cleaned.
So, where is the rust coming from? The rust spots that show up on the surface of the unit are not signs of the base stainless steel material corroding. Often, they are foreign material, such as welding slag, that has collected on the surface of the unit. The rust spots will be located around areas on the unit where there has been welding. It is not uncommon to find these spots around inlet and outlet connections of cooling towers, around coil connections of fluid coolers and condensers, around the cold water basin near the support steel, and around field-erected platforms and catwalks. Another possibility is that there may be dirt or airborne contaminants that contain mineral content that has collected in or on the unit. Given time and the right environment, this foreign material will rust and stain the surface of the stainless steel.
What can be done to get rid of these rust spots? A good cleaning should remove them. The cleaners that EVAPCO recommends are either Naval Jelly or a good stainless steel cleaner, such as Mother's Wax. Using a heavy-duty scouring pad, in conjunction with these products, will clean the surface of the stainless steel very well. In most cases, these means of cleaning the unit will correct the problem. It should be mentioned that maintenance of the unit's surface should be performed on a regular basis. The unit is just like a car; the finish must be maintained on a regular basis to preserve its appearance.
In areas where cooling towers are constantly exposed to a salty environment, rust spots may occur. At these locations, the towers’ exterior may require rinsing or wiping down once or more each year to prevent rusting and staining of the steel. There is also evidence that the presence of certain microorganisms/bacteria in system water may accelerate the breakdown of the steel surface if it is allowed to accumulate in the steel surface. Ask your local EVAPCO sales representative about the available water treatment options for your location.